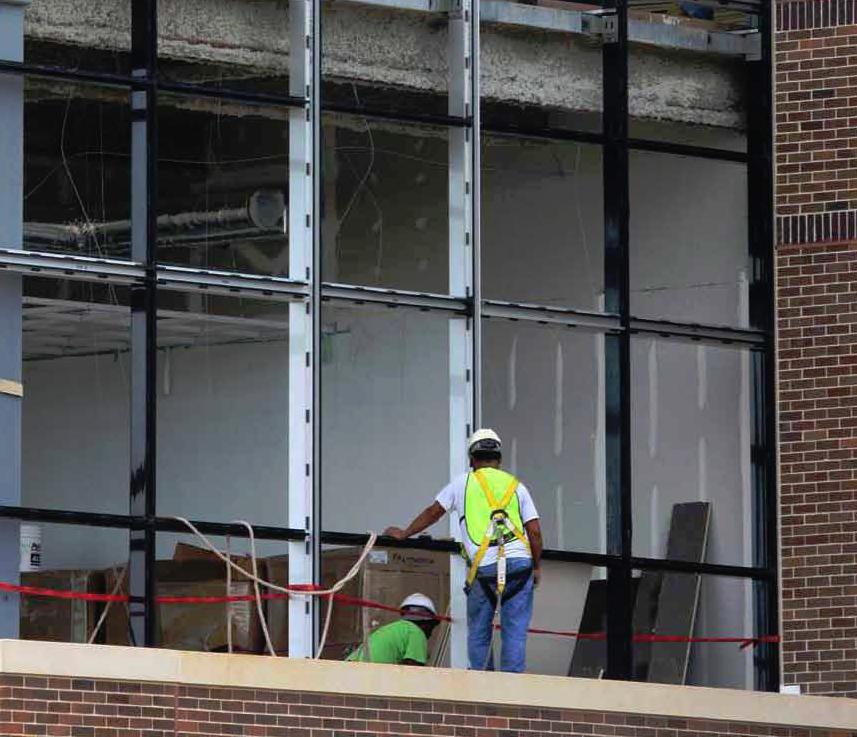
Driven by base realignments, lease considerations and homeland security concerns, a large-scale courtroom and office project at AndrewsAir Force Base was placed on the fastest of fast tracks. Keith Regan learns how the project team uses a design-build approach and constant communication to keep the project on its aggressive schedule.
When it is completed early next year, the Administrative Facility, known as the William A. Jones III Building, at Joint Base Andrews in Maryland, will house the United States Air Force’s only Appeals Court, the base trial court, many legal offices, numerous HQ Air Force staff offices as well as the Air Force District of Washington and 316th Wing staff. The building was named after William Atkinson Jones, III(May 31, 1922 - November 15, 1969) a United States Air Force Officer and a recipient of the United States military's highest decoration—the Medal of Honor—for his singularly distinctive action in the Vietnam War.
The 380,000-square-foot building consists of two five-story wings connected with common conference areas on each floor and features a host of green design and construction techniques. The project is planned to earn at least Silver certification from the US Green Building Council’s Leadership in Energy and Environmental Design (LEED) program, as well as enjoying a host of communications and security upgrades for the inhabitants of the Jones Building.
“It’s all about security,” says Susan Bench-Snow, Basing Division Chief, noting that the project is actually three in one, with BRAC 2005 driving one aspect and Air Force space needs the others. “It’s all about bringing people into an environment that is secure so they’re not out in leased space that might not be up to the same military standards that those on the base benefit from already.”
Because it stems from the 2005 Base Realignment and Closure Commission Report the construction of the facility and the movement of personnel into the facility are mandated by Congress to be completed by mid-September of 2011. However, as a number of key leases expire during this same timeframe, the project schedule has been accelerated to allow for a February, 2011 completion of significant construction work, enabling workers to move into the building beginning in March 2011.
The organizational moves into the facility will take several months. Behind organizational moves will be lease space remediation, where necessary, so that the Air Force is free and clear of the leases by the September 2011 timeframe. “We were fast-tracking the project right from the start,” says Bench-Snow. In order to facilitate the fast-track arrangement, Joint Base Andrews allowed the fencing off of the worksite, allowing all the workers and delivery vehicles direct access to the site, reducing delivery times.
This meant embracing a fast-track design-build model for delivery of the work. According to Jeff Pitchford, a project manager with design-build contractor CDM/CAPE (a joint venture of Cambridge MA-based CDM and Atlanta-based CAPE) the project was split into a number of design-build packages, starting with site work and foundation, then moving to structural components, building envelope and eventually to finishes and interior systems. Furniture layout, communications system support and electronic security systems became separate packages as well.
The first package, the foundation and site utilities for the project, incurred a slight delay as state permits were obtained, but ground was broken by the summer of 2009, less than six months after the design-build team was put in place. The commitment and approach taken by CDM/Cape enabled the project to get ahead of schedule once again by the summer of 2010. “We’re ahead of a schedule that was already very aggressive,” says Pitchford.
The construction schedule called for one wing to be enclosed first so that interior work could be shifted into that space while the other wing was still being constructed. By the end of June, 2010, some 400 workers were on the project on any given day—a number that was expected to peak at over 500 by late summer, when the project was slated to be brought to weather-tight status so that work could continue throughout the winter.
Coordinating this volume of work in a short time and small space requires the design-build team to keep close tabs on progress, including problems being encountered and any changes that might be necessary as a result. “We have a couple of very basic management principles and the most important one is to talk and talk and talk,” says Pitchford. “We are constantly engaging all our partners to go over everything that is necessary for the next day, week, month and longer. We are constantly trying to stay out in front of everything.”
Team cooperation is an essential element in addressing the daunting schedule. Key members of the team include engineers and designers from AECOM’s Northeast Washington DC office as well as Coakley & Williams Construction, a local contractor hired for its experience with building suburban office space. “The basic core of what we have is an office building,” Pitchford explains.
There will also be features that go beyond what is found in a normal office park. In addition to an enhanced security package, fitting for a military administrative facility and court, the entire building is being constructed with flooring that will cover and provide easy access and easy reconfiguration of the electrical, HVAC and communications systems. The space will also be wired with a passive optical network (PON) that brings fiber right to the desktop and which requires much less power (generating less heat and reducing the requirement for even more power for cooling) than a traditional network made up of powerful routers and switches.
The PON network installed throughout the facility will be the first of its kind for the Air Force and will be outfitted with Voice over Internet Protocol (VoIP) phones and secure networking functionality to allow workers to remain connected even if they are off-site. “We’re working on standards that will be based on this project and that will make it the norm to build this type of network,” says Charles Elmore, deputy director of communications for the Air Force District of Washington.
This network is just one of numerous sustainable features on the project. More than sixty percent of the roof area will be covered in a green roof and storm-water runoff collection system. A host of other construction-phase green techniques, such as using low VOC-emitting finishes and recycling construction waste, will be employed as well. “Those things are becoming standard in how we approach every project now,” says Pitchford. “Our goal on this project is to exceed LEED Silver and go for Gold. We want to and believe we can do that.” www.afncr.af.mil